Brewing environmental services
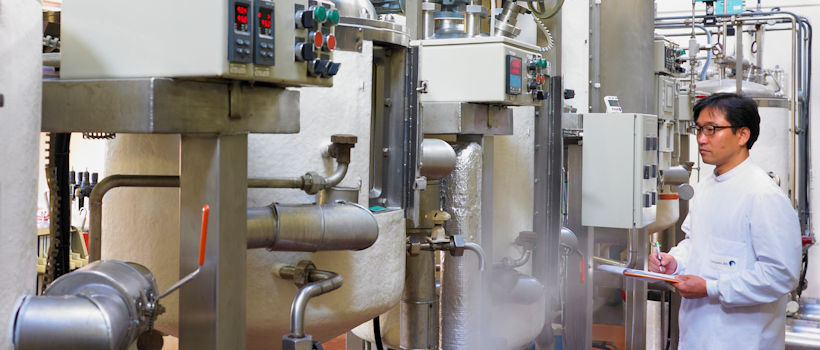
To discuss your needs
The brewing industry has an excellent record in recent years in improving its sustainable practices. Campden BRI support these achievements through application of:
- Highly skilled and knowledgeable staff that enable genuine process improvement
- A network of industry contacts that enable us to facilitate excellent projects and collaborations
- Excellent pilot and laboratory process facilities that have a track record of demonstrating novel process technologies and good practise
- Facilities to publicise success and support clients in their process aims
We have facilitated industry-leading benchmarks on environmental performance via key performance indicators. Brewers need to know how they rate in order to prioritise business plans.
- More benchmarks are planned to cover more process features such as technology selection.
- "Energy Saver" and "Water Saver" software packages, developed in association with KWA Business Consultants, enable brewers to reduce these KPIs through best practise guidance and investment appraisal
Other environmental services we offer include:
- Dissolved gas control
- Energy saver
- Environmental footprint
- Environmental protocols
- Thermal imaging
- Water saver
Dissolved gas control
We offer state-of-the-art expertise in current dissolved gas control technology, with a flexible service with keg-sized volumes processed at Campden BRI and small BBT volumes processed on-site. Our response is rapid and we offer professional back-up services in area of dispense and sensory to provide a complete package.
- Application of dissolved CO2/N2 combinations and oxygen removal for product enhancement
- Expertise in the use of hydrophobic membranes for the control of dissolved gases (CO2/O2/N2)
- A pilot scale gas control facility, incorporating a hydrophobic membrane
Energy saver
Campden BRI and KWA Business Consultants have developed a self-assessment benchmarking tool for energy use. This is aimed at brewery groups. It enables the user to- benchmark performance on process level, identify best practise and calculate energy and cost savings.
The key benefits are:
- it is based on Campden BRI and KWA's extensive experience of benchmarking energy use in the brewing industry and identifying energy and cost saving measures
- it can be customised to suit individual brewery groups needs
- it combines benchmarking and energy saving measures in single tool
The main features of Energy Saver:
- Basic data input: The user inputs production data, energy use (based on energy bills) and energy costs - this is used in subsequent phases to calculate the cost saving potential of possible measures. The programme calculates fuel consumption (MJ) and CO2-emsissions related to energy consumption.
- Energy distribution: This input sheet enables the user to allocate total electricity consumption and total fuel / heat consumption to the specific process unit operations in the brewery. Energy saving measures: The user can select from over 100 energy saving measures those that are viable and the software provides the opportunity to enter the energy saving calculations and payback times of the selected measures.
- Results group : The programme compares your results with a best practice plant (benchmark) that has the same configuration (production processes, marketing mix, location, etc.) as your plant. Results can be displayed for overall energy consumption or broken down into total fuel and total electricity use. Results can also be shown per process unit as tables giving the energy ratio compared to the best in class range, energy and cost saving potential and CO2 emissions. Data can also be shown as trend graphs or as a management report which enables a regular summary to be prepared for management meetings.
- Extra: this contains the manual and the backup facilities
Environmental footprint
With environmental issues climbing up the agenda and increasing pressure from the public and the government, organisations are forced to measure and manage their operations' impact on the environment. The task of collecting, standardising and analysing the environmental impact data across multiple sites can be difficult.Campden BRI offers assistance with your organisation's carbon and environmental footprinting.
We will:
- provide advice and support in collecting the required information across your operations including energy use, water use and waste generation
- standardise the data to make it comparable across all facilities
- validate the data eliminating possible errors in data collection and
- apply appropriate conversion factors to calculate your company's carbon footprint
We will also support you in the data analysis, identifying the most intensive areas of your operations, and help you with emissions and resource use reduction strategies.
Measuring your environmental impact is the first step to managing your resource use and identifying areas for reduction.
The benefits include:
- Understanding your organisations' material impacts
- Identifying which facilities perform better than others; internal benchmarking
- Making informed decisions about which reduction strategies to prioritise
- Being able to track your reduction progress
- Being able to report your organisations environmental footprint in your company's public communications
- Provide environmental information to your potential clients in tendering process and be able to prove that efforts are made to reduce your company's and your products' environmental impact
Environmental protocols
In 2006 Campden BRI with the support of the Grants Committee of the Institute of Brewing and Distilling produced a website which provides Protocols for the Auditing of Water and Energy Usage and Waste Management in the Brewing and Distilling Industries.
The protocols are to act as a guide to help breweries and distilleries who wish to carry out internal audits in their brewery or distillery. The suggestions can save on costs through improving processes and reducing energy and water consumption. There are also instructions for waste and emissions reduction.
The web site is split into Brewing and Distilling. You select the industry you are interested in, followed by the area you wish to focus on. You may then go through the suggestions for each process.
To visit the web site please click here
Thermal imaging
Thermal imaging is an established technology that is commonly employed in domestic premises and electrical installations. It is used to identify areas of energy wastage, perhaps an electrical system needs maintenance or a wall needs improved insulation.
However, We have identified the potential for application of thermal imaging to brewery and malting production processes. Some parts of the process are complex and it may not be a trivial task to identify places that are inefficient in terms of heating or cooling. However, a thermal imaging camera makes identification of hot spots and cold spots simple.
There is also benefit in a knowledgeable brewer or maltster applying the thermal imaging equipment. Many parts of the process benefit from quite accurate temperature control, and thermal imaging may identify areas where this does not occur. Also, the most likely areas for inefficiency can be focused on.
We have a thermal imaging camera that may be employed at clients' sites to improve energy efficiency. Look at this gallery for examples of images and the conclusions that can be drawn.
Water saver
KWA Business Consultants have developed a self-assessment benchmarking tool for water use. This is being marketed by Campden BRI.
It helps you to establish a standardized water balance on a process-unit level and compares your performance on water use to best in class values for the brewing industry. It will assist you to find hotspots in your brewery where you can save water and costs.
The key benefits are:
- it is based on Campden BRI and KWA's extensive experience of benchmarking water use in breweries
- it is a self assessment tool and is developed in easily accessible MS Excel software
The main features of Water Saver
- You will receive a copy of the Water Saver software to be used by your brewery only.
- You enter data for water use. This can be existing data, data from an internal water metering projects or estimated data (although this is less precise). If data on water use is readily available then it will take just a few hours to fill in the form.
- Water Saver immediately shows your water balance on a process-unit level so that you can see how much is used in each operation.
- The completed software is returned to KWA and your data is compared with best-in-class values (calculated from the data of several anonymous breweries, existing KWA / Campden BRI expertise and literature values).
- KWA sends you a report to compare your performance with best-in-class values for the brewing industry. This will give the gap analysis and indicate your water saving potential.
- You can then use this to make decisions on water saving projects in your brewery.
Key services
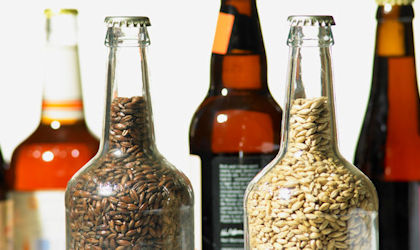
Beer, barley and malt analysis
Standard analyses and due diligence analyses for beer, malt and barley.
Submit a sample
For guidance on how and where to send samples, please see our sample guidance page
Brewing training courses
Explore our brewing related courses including; Brewing – an introduction and HACCP for craft brewers
Where we refer to UKAS Accreditation
The Campden BRI group companies listed below are accredited in accordance with the recognised International Standard ISO17025:2017 by the United Kingdom Accreditation Service (UKAS). The accreditation demonstrates technical competence for a defined scope of methods, specific to each site, as detailed in the schedules of accreditation bearing the testing laboratory number. The schedules may be revised from time to time and reissued by UKAS. The most recent issue of the schedules are available from the UKAS website www.ukas.com. Campden BRI (Chipping Campden) Limited is a UKAS accredited testing laboratory No. 1079