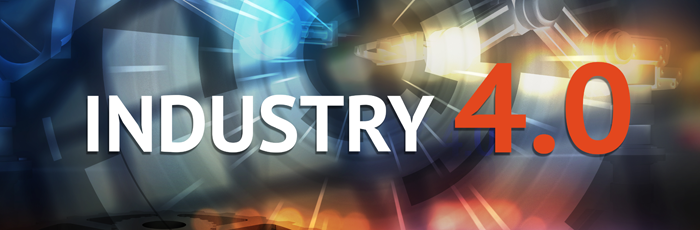
The digitisation of processing – what role does Industry 4.0 play?
12 July 2021 | Zsófia Kertész, Development Engineer at Campden BRI Hungary
Meeting the consumers’ needs and demands in a profitable way is one of the greatest drivers behind development and innovation in the food industry.
Responding to these demands, however, can be quite a challenge. Not only can they change rapidly due to unforeseen events (the impact of COVID-19 on consumer behaviour being the prime, recent example), but there are also the emerging trends and segments that need to be considered and prepared for if a food business wants to continually meet the consumers’ expectations.
Alongside this, there are many legal requirements for the food industry (or food business) to consider, including European, EU Retained legislation and National domestic legislation, particularly now the UK has left the EU single market. Legislation changes frequently as a result of an increase in knowledge, response to incidents and science innovation. Applying Industry 4.0 can enable food companies to respond to these rapid changes promptly.
In some ways, Covid-19 has appeared to have sped up innovation as businesses have been put under pressure to save on costs, and this is just one reason why it’s believed automation will be increasingly sought after in a post-Covid world. But before we delve further into how Industry 4.0 will help the food sector, it’s important to first clarify what it is exactly.
Industry 4.0 and digitalisation is about the efficient organisation of food production processes through fully-integrated collaborative systems that respond in real-time to meet changing demands and conditions in a food factory.
What is meant by Industry 4.0?
The Fourth Industrial Revolution is the ongoing automation of traditional manufacturing and industrial practices, using modern smart technology such as artificial intelligence (AI) and digital twin.
More specifically for the food sector, Industry 4.0 and digitalisation is about the efficient organisation of food production processes through fully-integrated collaborative systems that respond in real-time to meet changing demands and conditions in a food factory.
Putting it in perspective
Manual activities are important and frequently used in the food processing industry and reasonable decisions based on human thinking, knowledge, experience, attention and deliberation are important for reliable and efficient food production. However, a number of mistakes can result from human error, including distraction, tiredness, loss of attention, limitations in vision, perception and inaccuracy of manual settings, the time required for human intervention and limitations of recognising complex relationships.
Digital solutions can help to prevent and eliminate errors in many areas and may well complement manual activities and human perception, decision making and intervention. Therefore, the implementation of these applications can result in the production of better products and more accurate process control.
Benefits of applying Industry 4.0
As mentioned, it's true that applying Industry 4.0 can enable food companies to respond to rapid changes that occur in the industry, but I’ve seen with our work at Campden BRI that there’s more to it than that. The benefits of automation alone can be potentially quite substantial for food businesses that are willing to incorporate it into their factories. Take meeting supply and demand as an example. Big data (which is what it sounds: data sets too large to be dealt with by traditional data-processing software) can be used alongside computational tools to predict actual consumer demand. Combining big data with the use of smart sensor systems in food factories can optimise production to make machine-powered processes more efficient, ultimately reducing raw material use, energy consumption and CO2 emissions.
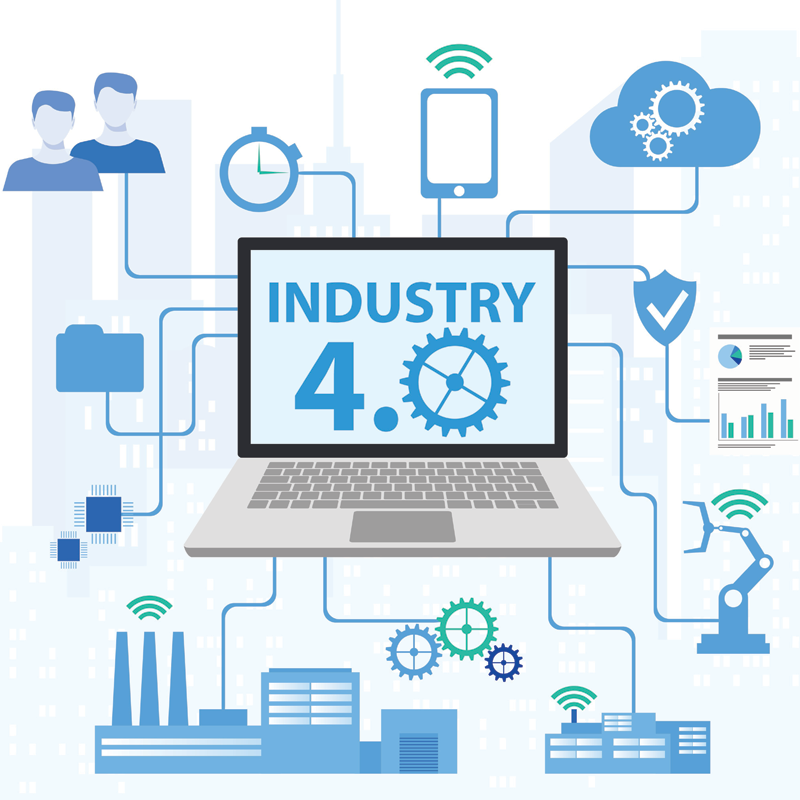
Case in point
Previously, as part of a long-term technology upgrade initiative led by our team at Campden BRI Hungary, we’ve seen success with the introduction of sophisticated controls. For example, the mechanical controls on the bread line of a traditional Hungarian SME bakery were upgraded with networked sensors and process monitoring software to reduce process variability, losses and the need for frequent quality checks. As a direct result, the uniformity of the bread weight and quality improved, ways to save on energy costs were realised and the throughput of the line improved by 5%.
How was this possible? The process monitoring system collected sensor data every few seconds as the line was in operation and sent out a detailed analysis of the previous day to the management. This guaranteed that bread defects and product complaints could be investigated, the origin determined, and re-occurrence avoided.
More broadly, digital solutions can help food companies in a number of different ways to help them achieve goals and targets, for example:
- Improving product quality and food safety
- Reducing waste and use of fewer resources
- Enabling a more flexible production and quicker response to changing product specifications
- Optimising the production processes
- Increasing the reliability in repetitive processes
- Reducing the number of failures
- Improving the quality of working conditions
- Providing new job functions and requirements for new skills, and
- Providing new career paths.
Getting the food sector up to speed with Industry 4.0
A survey conducted by the Digital Transformation Scoreboard in 2017 found that 74% of food companies had invested in digital technologies to improve production processes. Yet, some would say that the food sector still lags behind other industries when it comes to the uptake of Industry 4.0.
Despite the food sector being the largest manufacturing industry in the EU with an estimated €1.2 billion turnover, it is far behind other industries when it comes to digital transformation. This is a big, unexploited opportunity because many of the available solutions in other industries can be adapted to solve food problems relatively easily.
This is not to say the Fourth Industrial Revolution isn’t coming to the food industry. It’s just that there’s a lack of skilled people to make the adaption happen.
Zsófia Kertész, Campden BRI Hungary
z.kertesz@campdenkht.com
00 3614 331488
Industry 4.0 projects
Find out more about our Indsutry 4.0 projects; contact the author:
Expert-led training courses
Our training courses are delivered by industry-leading experts that get you up to speed with the food sector’s current challenges. From food technology to thermal processing, discover your perfect course today.